Sustainability In The Apparel World - Part II
August 10, 2023
We previously examined the apparel industry’s overall impact on our environment. Let’s now focus in on a smaller but important part of the industry - apparel decoration and screen printing inks, in particular.
Today’s market is dominated by three types of inks – water base, plastisol and acrysol. Is one greener than the others? It’s complicated – here are some facts to consider.
Water Base Inks
A common misconception is that water base inks are the most environment-friendly (and benign) choice since they are largely water and contain natural ingredients. Not so - water base inks, like plastisols and acrysols, rely on plastic polymers, pigments, fillers and various chemical additives.
Water base inks are widely used around the world. They traditionally consist of 20 to 70% solids. These solids include binders (usually an acrylic or urethane), pigments, fillers and additives. Water base inks rely on solvents that evaporate off leaving the pigmented binder compounds (the solids) on the garments. While the primary solvent is water, water base inks often contain co-solvents such as alcohols, glycols and acetates, as well as retarders and mold inhibitors. These co-solvents may put printers at risk unless they are properly protected from the evaporative fumes.
Plastisol Inks
Plastisols are also used widely around the world and because of their ease of use, are the inks of choice in North America. Plastisols are considered 100% solids, which means they provide virtually a 100% yield. They contain plasticizers that cross-link with the PVC plastic resins and become part of the ink film. Plastisols don’t evaporate and they don’t cure until they are heated; so plastisols don’t dry on the screen.
Acrysol Inks
Printers looking for an alternative to PVC and water base inks are looking to acrylic ‘acrysol’ inks as an easy-to-print option. Like plastisols, acrysols are 100% solids and provide the same high yield. They also behave and print just like plastisols – no evaporative fumes, no drying in the screen and no need to flash after every screen. So which ink is the most environment friendly? Hard to say without also considering the printing, handling and disposal processes involved with each of the inks. Determining the environmental impacts and sustainability of any material is complex. We touched above on the differences between the major screen print ink types – water base, plastisol, and acrysol. Let’s look now at how the processes involved with printing those inks can impact our environment.
Water Base Ink Processes
Water base inks consist generally of 30 to 80% liquids (water and other solvents). These liquids evaporate off during curing, leaving the solid plastic binders, pigments and additives on the apparel substrate. Energy is required to drive this evaporation and the venting of the fumes. Water base inks generally require a flash after each color, so more energy is needed to power the flashes and drive larger print machines (more flash stations). Water base printing also usually requires higher dryer temperatures and longer dwell times to assure complete curing. Water is an increasingly precious resource. Water base printing consumes water, not just for the inks, but for production (for example, mist sprays for humidity control) and daily cleanup of the screens. The misperception that water base inks are harmless because they’re largely water and contain natural ingredients leads to practices that may harm printers and the environment. Solvents and chemicals released during curing can contribute to air pollution and be harmful to a printer’s health unless precautions are taken to avoid inhalation of fumes. Printers may also mistakenly assume that water base printing wastes can be poured down the drain or into the environment.
Plastisol & Acrysol Ink Processes
Plastisol and acrysol inks provide a virtual 100% yield when printed. What’s printed on the garment remains on the garment. These inks contain little if any volatile materials, so there are little if any fumes escaping during the cure process.
Plastisol and acrysol ink printing generally consumes less power than water base printing. Since the inks are considered 100% solids, plastisols and acrysols don’t require the extra energy needed to evaporate off liquids. Plastisol and some acrysols can be printed wet-on-wet, so they don’t need to be flashed after each color. Fewer print stations are needed, and less energy is required to power the print process. Many plastisol inks can now be cured at temperatures as low as 275°֩ F (135° C) which further reduces energy consumption.
Plastisol and acrysol printing tend to generate less waste than water base printing. Plastisol and acrysol inks don’t cure unless they’re exposed to heat and there is little if any liquid that evaporates off the inks. Consequently, there is no need to clean screens daily. The inks can be left on the screen or put back in the bucket at the end of a print run.
Looking Forward
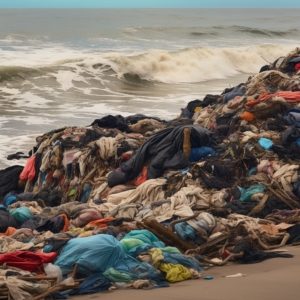
As we explained, the industry consumes tremendous amounts of increasingly precious resources, and produces billions of tons of waste every year. One dumping ground for discarded clothes, the Atacama desert in Chile, is visible from space1; and piles reaching 65 feet (20 meters) high line the beaches and city limits of Accra in Ghana. 2
There is good news emerging. Many apparel manufacturers, brands and retailers have begun to explore ways to reduce the environmental footprint created largely by throw-away ‘fast fashion.’ H & M, one of the companies at the forefront of fast fashion, recently launched an in-store recycling program in Hong Kong, where machines create new garments from old ones. 3
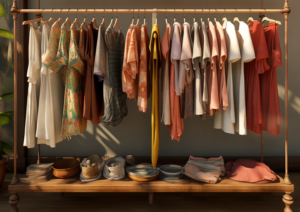
Can sustainable practices completely address the economic demands of a $1.5-trillion industry? Perhaps not yet, but ‘fashion-shaming’ is helping create new market spaces and companies misrepresenting their products’ eco-friendliness are increasingly being called out for ‘greenwashing.’ Demand for digital stores offering ‘gently-used’ clothing appears to be increasing, and “upcycling” is becoming a new industry buzzword. thredUP, a digital consignment and thrift store, is fighting fashion waste by reselling and extending the life of everyday clothes. The RealReal, another digital commerce site, resells authenticated luxury clothing and other goods.
Ideally, the apparel industry (and all industries) should strive for circular product lives. Garments should be manufactured in a resource-efficient manner and designed to have an extended life; and then have an after-life through reuse and recycling. The road ahead is challenging, but our industry is beginning to take the steps necessary to assure a more sustainable future. Recognizing the scale of the challenge is the necessary first step; and fortunately, one that is now receiving attention.
1Space.com
2Independent.co.uk
3Insider Business, YouTube
4The Guardian